Understanding the Process Behind Professional Packaging Machine Repair
Understanding the Process Behind Professional Packaging Machine Repair
Blog Article
Quick and Reliable Product Packaging Maker Repair Work Services to Decrease Downtime
In the affordable landscape of manufacturing, the effectiveness of packaging procedures hinges on the dependability of equipment. Quick and trustworthy repair services are crucial in minimizing downtime, which can lead to significant operational obstacles and economic losses.
Significance of Timely Fixes
Prompt repair services of product packaging devices are important for preserving functional effectiveness and lessening downtime. In the hectic atmosphere of manufacturing and packaging, even minor malfunctions can result in considerable delays and productivity losses. Dealing with issues quickly guarantees that devices operate at their optimal capacity, thereby guarding the circulation of procedures.
Additionally, timely and normal upkeep can avoid the escalation of minor problems right into major break downs, which frequently sustain greater repair work expenses and longer downtimes. A proactive strategy to maker repair work not only maintains the integrity of the equipment yet likewise enhances the total dependability of the assembly line.
Furthermore, prompt repair services add to the long life of packaging equipment. Equipments that are serviced immediately are less most likely to deal with too much deterioration, allowing businesses to optimize their investments. This is specifically essential in sectors where high-speed packaging is essential, as the need for regular efficiency is paramount.
Advantages of Reliable Provider
Reliable company play a pivotal function in ensuring the smooth operation of product packaging devices. Their proficiency not only improves the efficiency of repair work yet additionally contributes significantly to the long life of equipment. Trustworthy provider are furnished with the technical understanding and experience needed to detect problems properly and apply effective remedies rapidly. This decreases the threat of recurring problems and ensures that devices operate at ideal efficiency degrees.
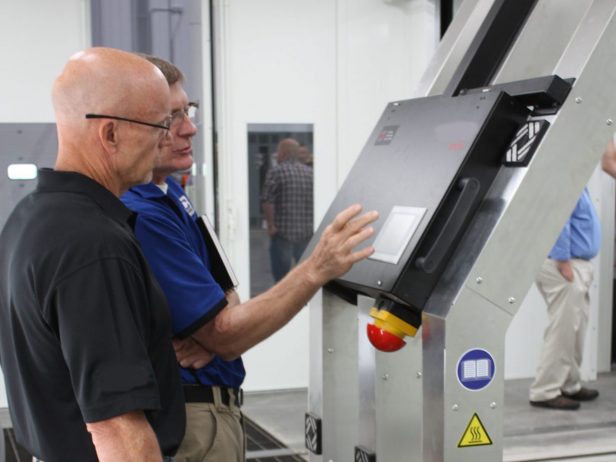
In addition, a trusted service supplier uses detailed assistance, including training and support for personnel on maker operation and maintenance best practices. This not only equips workers however also cultivates a culture of safety and security and performance within the company. Overall, the advantages of involving trusted provider prolong beyond instant repair work, positively impacting the whole functional workflow of packaging procedures.
Usual Packaging Device Issues
In the world of product packaging operations, numerous issues can endanger the efficiency and performance of machines (packaging machine repair). One more common concern is misalignment, which can trigger image source jams and irregular packaging, influencing item quality and throughput.
Electric troubles can additionally interrupt packaging procedures. Damaged wiring or malfunctioning sensing units may lead to irregular machine actions, triggering hold-ups and raised operational expenses. Additionally, software program problems can impede the device's programming, resulting in functional inefficiencies.
Irregular item flow is another critical concern. This can emerge from variations in product weight, shape, or dimension, which might impact the device's ability to handle items accurately. Lastly, inadequate training of drivers can exacerbate these issues, as inexperienced personnel might not identify early signs of malfunction or may abuse the equipment.
Dealing with these typical product packaging device problems without delay is necessary to maintaining performance and ensuring a smooth operation. Routine inspections and positive maintenance can considerably reduce these concerns, promoting a trustworthy packaging setting.
Tips for Reducing Downtime
To decrease downtime in product packaging operations, carrying out a positive maintenance technique is essential. On a regular basis arranged maintenance checks can identify prospective problems before they escalate, making sure devices run efficiently. Developing a routine that consists of lubrication, calibration, and evaluation of critical elements can significantly reduce the regularity of unanticipated break downs.
Educating personnel to operate equipment correctly and recognize early indication of breakdown can additionally play an essential role. Empowering drivers with the understanding to execute standard troubleshooting can avoid small issues from causing significant delays. Furthermore, preserving an efficient supply of essential spare components can expedite fixings, as awaiting components can result in extended downtime.
Additionally, recording maker efficiency and maintenance tasks can aid identify patterns and frequent troubles, permitting for targeted treatments. Including advanced surveillance technologies can provide real-time data, making it possible for anticipating maintenance and reducing the threat of sudden failures.
Finally, cultivating open interaction in between drivers and upkeep teams makes certain that any type of irregularities are immediately reported and attended to. By taking these positive actions, businesses can improve functional performance and significantly minimize downtime in packaging procedures.
Selecting the Right Repair Work Solution
Picking the suitable repair service for packaging equipments is a critical decision that can significantly influence functional performance. Begin by evaluating the service provider's experience with your details type helpful hints of packaging tools.
Following, think about the company's track record. Looking for feedback from various other businesses within your sector can offer understandings into reliability and top quality. Certifications and collaborations with recognized devices suppliers can likewise show a commitment to quality.
Additionally, examine their response time and accessibility. A provider that can provide prompt assistance decreases downtime and keeps production circulation steady. It's likewise critical to ask about guarantee and solution warranties, which can reflect the confidence the copyright has in their work.
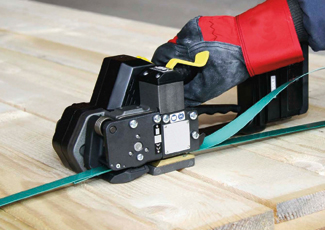
Verdict
Finally, the relevance of quick and reliable packaging machine repair service services can not be view it overemphasized, as they play a vital role in decreasing downtime and making sure functional performance. By focusing on timely fixings and choosing dependable company, services can efficiently keep and deal with usual issues performance. Implementing proactive upkeep practices and purchasing staff training more enhances the durability of product packaging equipment. Eventually, a strategic strategy to repair services fosters an extra resilient production atmosphere.
Timely repair work of product packaging equipments are crucial for maintaining operational efficiency and reducing downtime.Additionally, prompt fixings add to the long life of product packaging equipment. On the whole, the advantages of involving reliable solution carriers expand past prompt fixings, favorably affecting the whole operational workflow of product packaging procedures.

Report this page